This paper proposes a theory to explain how rural sociality has influenced workforce behavior and productivity at a Global Manufacturing Systems’ automotive assembly plant in mid-Michigan. The paper argues that for over 100 years, rural and farming families in the region have been appropriating GM factories in order to sustain their rural life ways and remain part of their own ‘moral’ community. Loyalty to the company is conceptualized from the families’ perspective as a requirement of sustainable communities, motivated by an intergenerational desire to keep GM in Michigan. Employee loyalty also benefits the company by ensuring high performance and quality. The link between sociality and performance is illustrated through statistical modeling of attendance data and maps produced through ArcGIS.
BACKGROUND
In this paper we provide a theory to explain how rural sociality has influenced workforce behavior and productivity at General Motors’ (GM) Lansing Grand River (LGR) assembly plant. LGR was the first facility in North America designed around GM’s Global Manufacturing System (or GMS). The heart of GMS is lean production, the elimination of waste1, and the standardization of practices as a basis for continuous improvement. GMS provides a set of both high and low technology tools that permit employees to participate in taking waste out of the manufacturing system. LGR produces the Cadillac CTS, CTSV, SRX, STS, and STSV models, which are all based on a common architecture. Since the plant began production in 2001, its products have had notable success in the marketplace, and the plant has emerged as a leader in quality luxury car production in the U.S. market. In the 2004 J.D. Power and Associates Initial Quality Study, vehicles produced at LGR ranked the highest in North and South America, and third in the world, for initial quality2. In 2005, the Harbour Report named LGR the ‘benchmark’ (best in class) plant for luxury vehicle production. There is great interest by a number of stakeholders as to the source of this success, and the competitive advantage it conveys to the Cadillac brand. Our research revealed a link between sociality and worker performance.
Our study began as an industry-university partnership. The university team included scholars from Michigan State University’s (MSU) School of Labor and Industrial Relations (SLIR), Eli Broad Business School, and Department of Anthropology. LGR Human Resource (HR) management was interested in the project because it promised to tell the story of LGR’s success, and the plant’s unique technological and “people system” that had never before been documented. There were various hypotheses regarding the plant’s success. Our SLIR colleagues thought the success derived from the unique collective bargaining agreement between the UAW Local 652 and LGR. The anthropologists focused on the cultural, historical, and community-based roots of the cooperative union-management relations and special “people system” at the plant. We began to explore our hypotheses in 2004 with a volunteer sample of 54 employees that we engaged in personal interviews and three focus groups, as well as direct observation in the plant, and participant observation during GMS training. Our interviews revealed a ‘native hypothesis’ for the plant’s success. Both hourly and salaried workers told us that the plant’s success should be attributed to the values that had been instilled in the workforce during their socialization in the mid-Michigan area surrounding the plant, particularly experiences that workers had within rural and farm-based families. Our interviewees described several interrelated characteristics of the workforce that they believe were instilled during socialization in a rural community. These included: discipline, punctuality, dedication to long hours, commitment, loyalty, pride in quality, and the desire to “do the right thing.” Their ‘native hypothesis’ was that the plant benefited from their rural sociality which taught them that in order to succeed one must a) show up to work, b) work hard while there, and c) make a quality product.
A PLACE-BASED THEORY OF COMPETITIVENESS
The ethnographic data led us to theorize a place-based model of competitiveness. We postulate a link between three place-based propositions, the combination of which has direct implications for productivity. These include: 1) socialization in a Midwestern, rurally-based family/community instills particular norms and values which persist to form a key part of one’s identity (these norms and values were itemized above); 2) working at a plant with others who also have been socialized in the same manner (either relatives or management, or both) re-enforces and enforces expected normative behavior (e.g., family policing); and 3) members of the workforce choose to continue living within these rural communities, creating a loyalty to other community members, and generating an on-going incentive to sustain their place of employment, which in turn sustains the viability of a rural life-style. The following three quotes illustrate these propositions.
Us from the smaller towns, basically we do our jobs and we’re more patient, more disciplined on how to get there…we’re more disciplined in our culture. It’s because the way we were raised. I had a lot of morals instilled in me growing up. I learned really quick in life that there’s rules and you have to follow rules, and there are always repercussions if you don’t. I come from a disciplined household.
If your father went to work every day, you more or less did too and if you didn’t, he jumped on you maybe more than your boss ever did. I think it made us a little more aware of [being] fortunate to have a good job, fortunate to have to go to work.
The town I’m from [has] a very high percentage [of people who] work in the automotive industry…and I think that’s an issue too because I myself feel a lot of pressure living in that environment, knowing – I guess you have a loyalty – you know all your neighbors and family members rely on the business that is sustained over the years. Versus if I move to California and work at a plant for two years knowing that I’m leaving. The commitment, the loyalty, I think, is not there. It [moving for work] is more personal interest versus I know I’m living there forever and I’m surrounded by people that work in that industry and I’m going to do my best to make this thing work.
Based on our interviews, we postulated that rural workers want to remain a part of their geographically based community because they believe rural sociality is responsible for their “good” and “moral” qualities, but they need external economic resources to sustain their rural way of life. The workers appeared to have sacralized the places in which they were socialized. We hypothesized that their loyalty to their home communities motivated them to ‘hold the plant down’ with an exceptional work effort that has direct implications for productivity and quality in the plant. We conceptualize the relationship between these rural families and the industrial plant as one of loyalty, but not traditional corporate loyalty that has been presented in the literature as a top-down management strategy.
Continuing social bonds, both within intergenerational families and in small communities, place pressure on their members to engage in practices that will ensure that neighbors and families can sustain themselves. Loyalty thus has a community or family origin and a localized, situated or ‘rooted’ nature, since it depends upon actual and presumed continuity of social relationships. We postulate that bonds of loyalty within the community are transferred to the plant through a strong work effort, one that enables the plant to be sustained so that the community can be sustained. LGR and General Motors benefit from this transference of family and community loyalty, which translates into high productivity and high quality products. The transference of loyalty is a mechanism through which the community exchanges its resources for those of the plant in a form of local-global symbiosis, where both parties gain something that neither could gain alone, resulting in economic competitiveness for the region.
METHODS
When we told HR personnel (many of whom were from rural Michigan themselves) about this theory, they became interested in supporting us so that we could test it. It was at this time that we expanded our research team to include expertise to facilitate statistical analyses and GIS to visually represent our findings. HR granted us increased access to demographic and performance data for the entire plant population. Moreover, they facilitated a mail survey with the entire hourly population (n= 1685) to garner information about location of employee socialization. We received a 27% response rate.
We have two different geographic databases: 1) the current residences of 100% of the hourly workforce, and 2) the location of socialization for 27% of the hourly workforce (i.e., 454 of the 1685 workers responded to the mail survey). Comparison of worker current residence with the survey data collected on place of socialization showed us that the places people were talking about in our interviews are places where workers still reside (50% of the workforce currently live in “rural” Michigan).3 Survey and interview data also suggest that many other workers who were socialized in rural Michigan currently reside in urban areas. The following map visually displays the current geographic distribution of LGR’s hourly workforce. The map was produced through a process called “geocoding,” which creates map features from addresses. The orange points reflect the current mailing addresses of all hourly employees.
In order to test the hypothesis that rural workers have higher performance levels than urban workers, we are conducting statistical analyses on the relationships between five performance areas and the geographic place (“rural” or “urban”) of worker residence as well as the geographic place of socialization. Worker performance is tracked in five areas by LGR, known as the PSQRC metrics. These performances areas are: 1) People, which is an attendance log; 2) Safety, a record of lost workdays and on-the-job injuries; 3) Cost, a log of wasted materials; 4) Quality, the degree to which expectations are met or exceeded; and 5) Responsiveness, operating under the short lead time principle (i.e., addressing problems and limiting assembly line downtime). Analyses are still in underway, but we do have some key conclusions for one of the performance metrics: attendance.
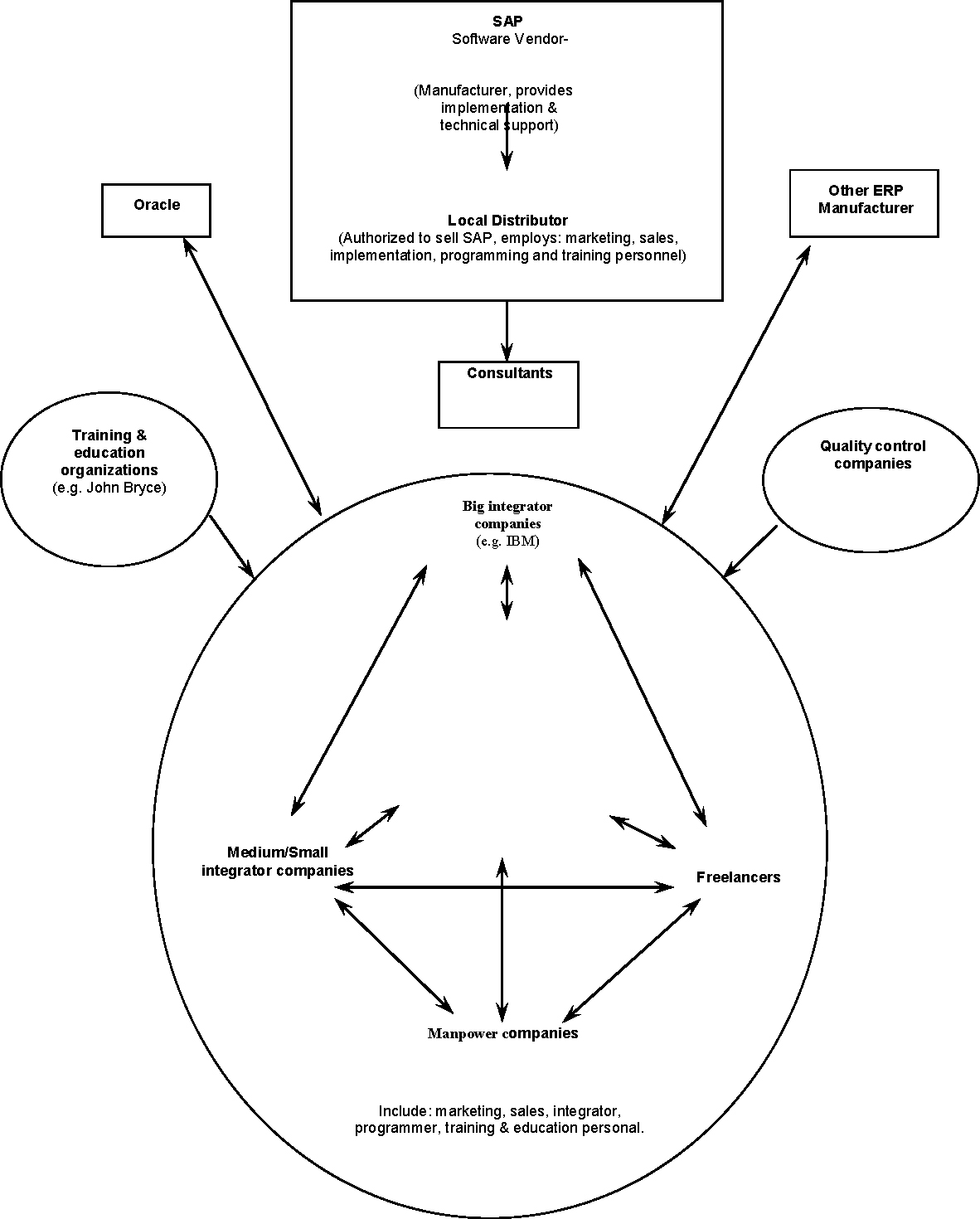
We selected attendance as the first section to analyze because it is arguably one of the most significant performance areas in a GMS lean manufacturing plant. The hourly workforce operates in teams comprised of 4-6 team members who rotate jobs throughout the day. The team is led by an hourly (i.e., union represented employee) team leader whose responsibilities include decision-making, job assignment, assistance with repairs, and taking over during bathroom breaks. Unlike traditional plants, facilities that run “lean” do not build in floaters (i.e., extra buffers in the hourly workforce to fill in for absent employees). Therefore, whenever a team member needs a bathroom break, requires help with a problem on the line, or is absent, the team leader must work on the line, prohibiting the team leader from fulfilling his/her normal duties. If the team leader is online, there are no other hourly workers (“floaters”) to step in for their co-workers for breaks or repairs. Help must come from the group leader, who is a salaried employee in charge of all teams within a work group (groups usually consist of 3-6 teams). If two members of a team are absent, hourly team members and team leaders and group leaders from other areas of the plant are temporarily reorganized to replace those absent. One can see from this description how as few as two unplanned absences could have a significant impact upon worker productivity and the overall quality of the vehicles.
Attendance is tracked at the individual, team, and group level: 1) HR personnel log individual attendance in two categories: 1) contractual absenteeism, or absences permitted within the GM-UAW collective agreement (e.g., bereavement, sick leave, vacation) and, 2) controllable absenteeism, or unplanned absences (e.g., the employee does not show up). We used year-to-date (January-July 2005) controllable absenteeism and perfect attendance records in our statistical analyses. Attendance is also monitored on a daily basis by the team leader and group level for both day and night shift.4 The data is recorded on oversized paper and hung on large poster boards throughout the plant. The fact that the plant has hourly workers track their own attendance and display it publicly for all to view even though attendance is already monitored by HR, forces mindfulness of work behavior and illustrates the significance of attendance in a lean manufacturing plant. We hypothesize that attendance is a key driver of productivity and should therefore affect other performance indicators.
FINDINGS
To test the hypothesis that workers from rural areas have better rates of attendance than workers from urban areas we ran a one-way analysis of variance (abbreviated ANOVA) with a 100% sample of hourly workers. The results of this test (Table 1) indicate that there is a significant difference in the net year to date absenteeism hours between rural workers and urban workers. The F statistic is equal to 3.846 degrees of freedom numerator = 1, degrees of freedom denominator = 1682) and is significant at .05 confidence level. On average, the 926 rural workers were absent for 17.52 hours, while the 758 urban area (and urban cluster) workers were absent 21.66 hours. As such, rural workers have significantly lower levels of absenteeism when compared to urban workers, leading us to reject our null hypothesis.5
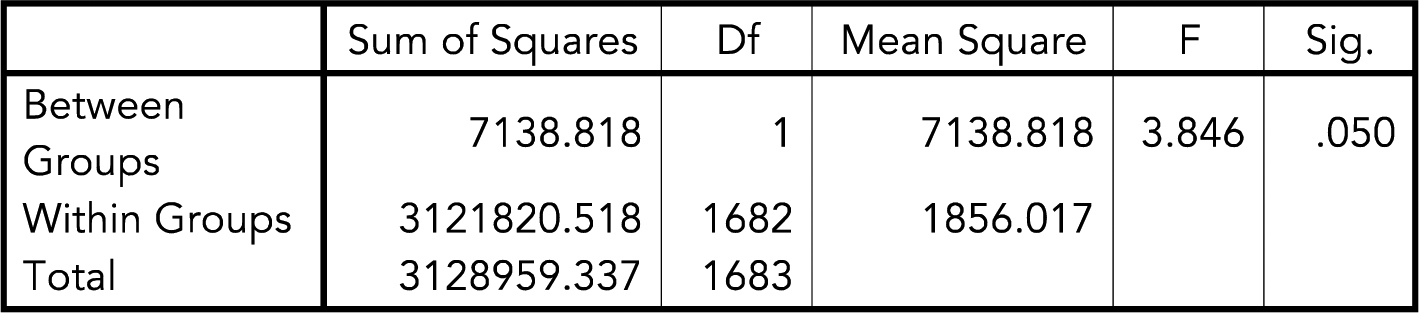
Table 1: ANOVA Results for Rural-Urban Attendance
Further, to determine the link between attendance and other factors, such as safety, a correlation analysis was performed using the PSQRC team performance. The results indicate a significant positive correlation (.192, p < .01) between perfect attendance and perfect safety. This suggests that attendance is a key driver of other performance metrics.
Analyses of the survey data (Table 2) support the results from the 100% sample, in that they revealed that rural workers have significantly lower levels of absenteeism than urban workers (significant at the .1 confidence level). The survey data enabled us to look at the relationship between attendance patterns and other variables, including differences for employees hired through referrals (as opposed to open hires), for workers who transferred from out of state (as opposed to individuals who spent their lives in Michigan), and for individuals who had a long daily commute to work.

Table 2: Logit estimates for the effects on perfect attendance
Note: control variable effects omitted from table
Our findings show that workers referred to GM have significantly better attendance than those who were hired through open-hires (significant at the .05 confidence level). Moreover, we found that individuals who transferred from out-of-state have poorer attendance habits than workers transferred from other places in Michigan (significant at the .01 confidence level). Further, the length of commute did not have a significant impact on worker attendance. All of these recent findings support our place-based theory of competitiveness. While we do not have concrete data, we speculate that most workers refer family or other members of their community for work in the plant. That referred employees have better attendance suggests a transference of loyalty from the community to the factory. Worker home communities could be nearly two hours away, but their loyalty drives them to make the regular commute without having a negative impact on their attendance. Our theory is further reinforced by the finding that transfers to the state have worse attendance patterns – their loyalty is not to mid-Michigan, but lies elsewhere.
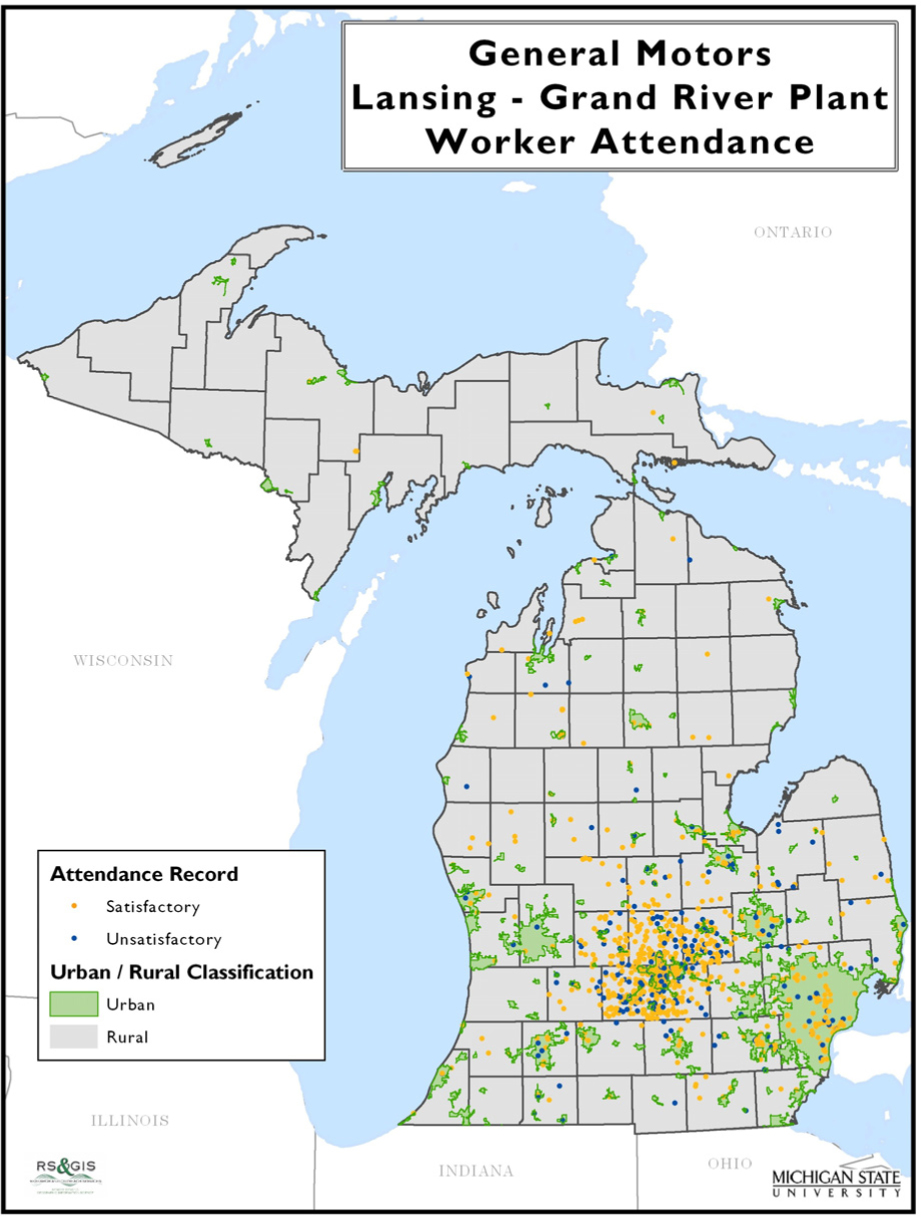
COMMUNICATING FINDINGS
To communicate our findings to management about rural versus urban sociality and attendance patterns we employed ArcGIS Desktop software. The figure to the right is an example of the maps we produced. It displays attendance data for the hourly workforce by placing dots on their current residence. We used year-to-date net percent absenteeism and applied the GM corporate standards for acceptable levels of absenteeism. Orange dots signify workers with an acceptable level of absenteeism (this category includes individuals with perfect attendance). Blue dots signify workers with an unacceptable level of absenteeism. The areas shaded in green are urban areas and urban clusters. While it is difficult to see in this map, when satisfactory attendance and unsatisfactory attendance are displayed on separate maps, rural and urban worker attendance levels are distinctive.
THEORETICAL IMPLICATIONS
Our conceptualization stands corporate loyalty on its head: loyalty also may emerge from below – from the generations of rural and farming families who comprise the LGR workforce. Loyalty springs from a geographically situated, ‘moral’ community of these employees, and from there it is transferred to LGR via a system of team-based work practices that share certain features with farm work (e.g., flexibility, discipline, dedication to hard physical labor and long hours). The workforce, in turn, obtains ‘loyalty’ from General Motors in the best way they know – with outstanding, globally competitive work that yields return on investment. In this scenario, the employees receive more than wages; they retain a way of life.
The following image models our theory.
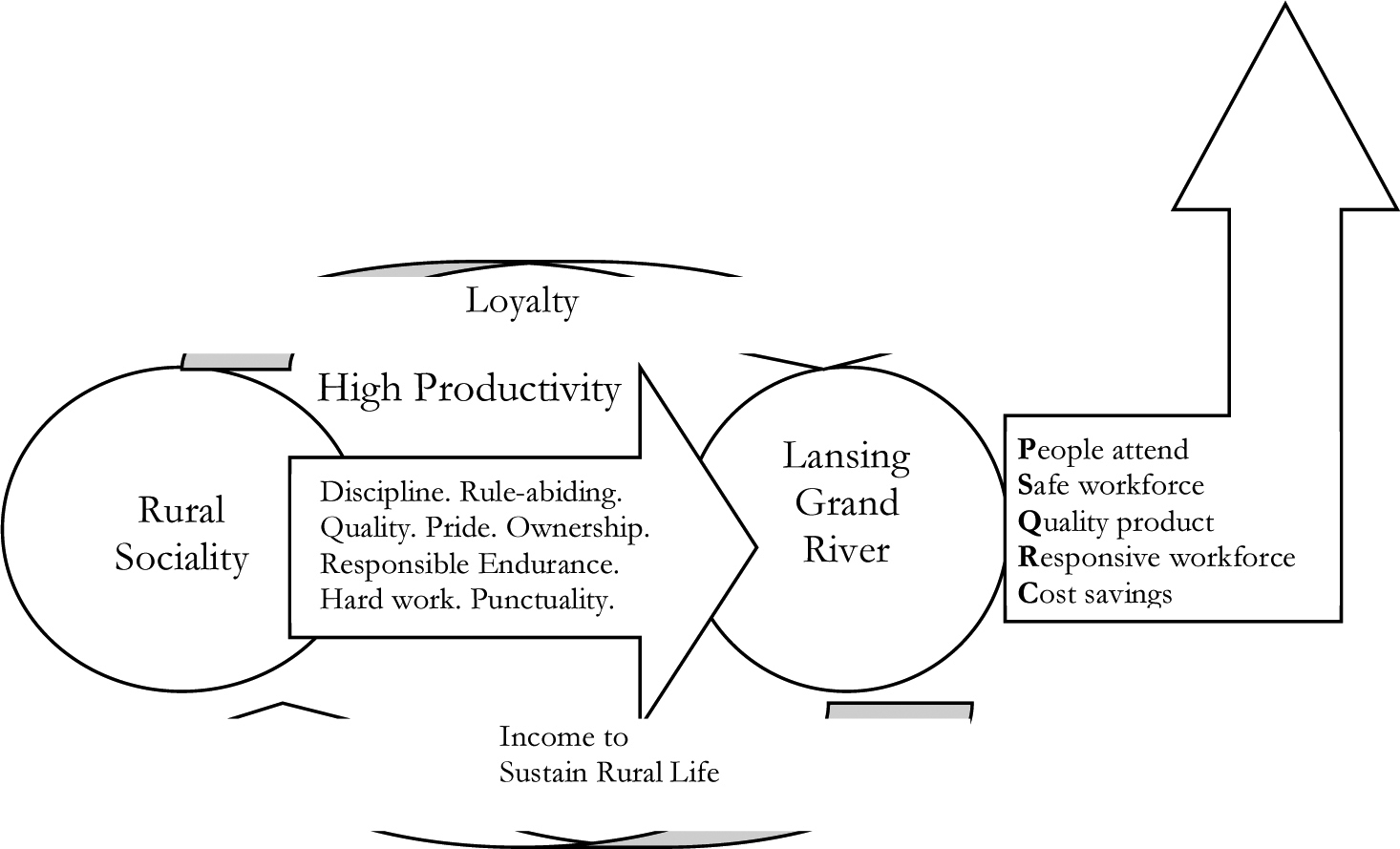
MANAGERIAL IMPLICATIONS AND LIMITATIONS
The findings of this initial study offer some potentially interesting insights for managers. One implication is that employees are motivated to comply with social norms. Therefore, it may be beneficial for the management at LGR to institute programs and activities that will help to instill a sense of community within the plant, particularly as new workers from other locations are transferred to the facility. Additionally, it appears that employees’ allegiance is to the community, rather than to the corporation or the plant. The findings suggest that the self-interest of the individual employees, who wish to maintain the nature of their community, drives their performance. The implication for managers is that integrating the plant with the community (through a variety of involvement initiatives), as well as clearly elucidating the joint destiny of management and workers, will help to ensure the maintenance of a high level of productivity and quality measures. Plant management should continue and their community-building initiatives, and it may be advisable for GM’s corporate group to pursue greater efforts along these lines to increase loyalty to the organization as a whole.
In order to add greater depth and breadth to the contribution of this study, a more in depth survey based on the development of latent constructs and survey responses of the entire plant population should be conducted. This ongoing study has been undertaken in the very limited context of one industry, and in one geographic location; therefore, the findings are limited in generalizability. Future studies can extend this research to other contexts, for the purposes of both comparison and extension of the conceptual development.
Keri Brondo is a Doctoral Candidate in the Department of Anthropology and Research Fellow in the College of Social Science at Michigan State University, and the project director for the Lansing Grand River study.
Marietta Baba is a Professor of Anthropology and Dean of the College of Social Science at Michigan State University, with an interest in processes of technological innovation within organizational contexts.
Sengun Yeniyurt is an Assistant Professor of Marketing at University of Nevada
Janell Townsend is an Assistant Professor of Marketing and International Business at Oakland University, with research interests largely focused in the context of the automotive industry.
Ethnographic Praxis in Industry Conference Proceedings 2005,pp. 196–204. © American Anthropological Association, some rights reserved.
NOTES
Acknowledgments – The authors would like to thank Mike Reinerth,Vickie Gaudard, Dan Wedley, Pat Lefevre and the employees of GM’s Lansing Grand River Assembly (LGR) plant for their participation and support of this study, and General Motors, who generously provided financial support through a GM Foundation Grant.
1 Reduction of waste is the responsibility of everyone in the plant: corrections-errors, overproduction, material movement, motion, waiting, inventory, processing (do what is necessary, but no more).
2 The J.D. Power and Associates study measures the number of problems consumers experience during the first 90 days of vehicle ownership.
3 We are analyzing our data using the 2000 Census classification for Urban and Rural territory. Urban Areas consist of an urban nucleus of 50,000 or more people with a population density of 1,000 people per square mile and associated area with a population density of at least 500 persons per square mile. Urban Clusters meet the same criteria as Urban Areas, but have populations of 2,500 to 49,999. All other territory is classified as rural. For the purpose of our analyses, we collapsed people from Urban Areas and Urban Clusters into one category of “urban workers” to compare with a second category of “rural workers.” We combined the two because the population of workers who reside in Urban Clusters (n=101) is too small to provide statistical significance when comparing with the populations of Urban Areas (n=653) and Rural Areas (n=641).
4 We have proprietary data that we cannot include in this paper that explains in more detail how attendance is tracked as well as GM corporate metrics regarding acceptable levels of absenteeism for the plant to run smoothly.
5 We were concerned about the racial implications of our rural sociality hypothesis, given the demographics of the plant population. Ethnic minorities comprise 20% of the hourly workforce and LGR is in full compliance with EEO and even has its own self-imposed affirmative action procedures for hiring women and minorities. Their goals are set based on the Standard Metropolitan Statistical Area and the plant continues to meet their affirmative action goals each year with regard to hiring women and minorities. Our statistical results indicate that there is no significant effect of minority status on attendance. One-way ANOVA results indicate an F statistic of .387 (degrees of freedom numerator = 1, degrees of freedom denominator = 424) for minority status and this is not statistically significant at a .10 confidence level. Minority workers have an average absenteeism of 13.43 while the non-minority workers have an average absenteeism of 17.71, but the difference is not statistically significant at the .10 confidence level. Although the comparison of the groups does not yield statistically significant results, we do see that ethnic minorities, on average, have relatively good attendance habits (i.e., a mean score of 13.43 hours missed year-to-date). Yet we did find that gender has a significant affect on attendance (women comprise 20% of the hourly workforce). The ANOVA results for the survey data indicate a significant effect of gender on attendance. The F statistic is equal to 8.117 (degrees of freedom numerator = 1, degrees of freedom denominator = 424) and is significant at .01 confidence level. On average, the 84 female respondents were absent for 29.40 hours, while the 342 male respondents were absent 21.61 hours. As such, among the survey respondents, male workers have significantly lower levels of absenteeism when compared to female workers. The relationship between gender and performance levels is a topic for further research and something we hope to explore in our next phase of the study.